物流業界が大きく変わろうとしています。ビッグデータ解析が行える人工知能や人間を追って自動で走るロボットの登場により、各企業で業務効率化が図られています。
2018年には、ニトリがロジスティクスロボットを国内で初めて採用し、大きな注目を集めました。ロジスティクスロボット導入で出庫効率が4倍になり、作業にかかる負荷を軽減できたことが報告されています。ニトリは人的コスト削減により、高品質・低価格の商品販売が行われています。
参考文献:日経ビジネス ニトリのロボット倉庫に潜入
物流業界は人材不足が問題視されているため、最新のテクノロジーを導入して時間やコストを抑えることが必要不可欠になりました。
ピッキング指示に課題を感じている方は、これを機にピッキング業務の効率化を考えてみてください。本稿では、ピッキング指示でよくある課題と解決方法をご紹介します。
ピッキング指示とは
ピッキング指示とは、出荷内容に従って、ピッキング作業者に指示をすることです。商品の保管場所・商品コード・数量等が記載されたピッキング指示書を使って指示を出します。
従来は、ピッキング指示書を紙に印刷する「リストピッキング」が採用されていました。しかし技術の進歩によって、ピッキング指示書のデジタル化が進んでいます。業務効率化が見込めるため、デジタルピッキングを採用する企業が増えています。また近年では、ロジスティクスロボットも登場しており、大手企業を中心に導入され始めています。
ピッキング指示の課題
ピッキング指示を見直す企業も多いですが、主に次のような課題を抱えています。
商品探索に時間を要する
物流倉庫の稼働率を高めるうえで、最も重要といわれるピッキング作業ですが、商品探索に時間が掛かるという課題があります。商品が品切れ状態で未補充の商品を何度も探したり、ピッキング指示書に商品を探索するための情報が不足していたりするのが原因です。
移動距離・時間が長い
ピッキングは、出荷オーダーごとに保管場所から商品を取り出す作業です。とくに、シングルピッキングでは、発送先ごとにピッキングを行うため、1回毎の移動距離が長くなりがちです。倉庫が広ければ広いほど、ピッキング作業全体に占める移動時間が大きくなるため、移動距離短縮方法の検討が必要です。
人的ミスが発生する
シングルピッキングでは、紙のピッキングリスト(出荷指示書)が使用されていることが多く、ピッキング作業者の経験を頼りにしがちです。ピッキング作業者によって作業のバラつきが生じ、人的ミスも起こりやすくなります。
作業スペースの確保が必要
複数の出荷オーダー商品をまとめてピッキングし、出荷オーダー毎に仕分けする作業方法をトータルピッキングといいます。トータルピッキングは全配送分の商品を集めるため、移動距離を短くできます。その一方で、仕分け工程が追加されるため作業スペースの確保が必要です。
ピッキング指示の課題解決方法
ピッキング指示の課題は、以下の方法で解決することができます。
品出し方法を変更する
商品の置き方を変更するだけでも、ピッキング作業の効率化を図ることができます。例えば、品出し時にケースを開口しておく、ピッキング作業者側に向けておくことなどが挙げられます。
品出し時の作業工数が増えますが、20個入りのケースであれば品出し作業の工数はプラス1、ピッキング作業の工数マイナス20です。このように全体のバランスを考えて工夫をするだけでも効率的になるでしょう。
ピッキングシステムを導入する
ピッキング作業を効率化するために、様々なシステムが登場しています。最もベーシックなピッキングシステムとして、バーコードリーダーがあります。最近ではRFID、デジタルカート、可動式棚などの新たなシステムが登場しており、導入する企業が増えています。
これらのシステムを活用することで、ピッキング作業の効率化が図れますので導入を検討すると良いでしょう。
ペーパーレスピッキングを導入する
ピッキングリストは、社内で使用する作業指示書です。外部資料ではないので、ピッキング作業が終われば処分されます。多品種少量生産出荷の倉庫では、ピッキングリストは大量のゴミになってしまいます。
またピッキング指示書を紙で印刷する場合は、印刷・配膳する時間も必要となるため、業務効率化でピッキングリストを発行しないペーパーレスピッキングを導入する方法がおすすめです。
副資材の使い方を見直す
ピッキング作業に梱包作業がある場合、作業性の高い緩衝材を使用したり、緩衝材の置き場所を工夫したりすることで作業は大きく改善されます。梱包作業が別工程の場合でも、その工程が詰まると後工程の処理待ちが発生する可能性があります。
製函機や自動梱包機などを導入して、前工程・後工程を効率化し、処理待ちを排除するのもピッキング作業の効率化のために必要です。
ロケーション管理を工夫する
在庫配置方法を工夫することで、ピッキング作業の効率化が図れます。在庫配置方法として「固定ロケーション」「フリーロケーション」「ダブルトランザクション」があります。
・固定ロケーション
固定ロケーションとは、決められた場所に商品を保管する方法です。商品ごとに保管場所を決めるため、どこに何を置いているかを覚えやすく、作業の効率化が見込めます。
しかし在庫がなくなり棚が空いても、他の商品を置くことはできないため、その場合収納効率は下がります。収納効率が悪くなっても、費用対効果の観点から多くの現場で採用されています。
・フリーロケーション
フリーロケーションは、流動的に保管場所を変える方法です。最短距離で空いている場所に商品を置いて保管していくため、スペースの有効活用ができます。
しかし、入庫情報を登録・共有しなければならず、作業効率が上がるとは限りません。多品種少ロットの商品展開が進んでいるため、フリーロケーションを採用する現場も増えてきました。バーコードやRFIDなどを活用したデジタルを利用したピッキングで、フリーロケーションの欠点を補うことができます。
・ダブルトランザクション
ダブルトランザクションは、ピッキングエリアとストックエリアを分割して運用する方法です。ピッキングエリアでは、出荷のためのピッキング作業を行います。ストックエリアでは、ケースやパレットなどの大きな荷姿で商品を保管します。
このように分割することで、ピッキングエリアに在庫を保管するためのスペースが必要なくなります。その分、通路幅や作業スペースに余裕が生まれ、移動距離も短くなるため作業効率化が見込めます。
AI分析で最適な商品配置を割り出すシステムも登場
ピッキング作業情報には、「誰が」「いつ」「どこで」「何に」「どれぐらいの作業を行ったのか」が含まれます。これらの情報をAIで分析することで、最適な商品配置を割り出すシステムも登場しました。
AIのディープラーニングは、膨大な量のデータから法則性を見つけ出すことだできます。そのため、これまでのピッキング作業結果を細かく分析して、最適なロケーション配置を割り出すことができるのです。
業務効率化におすすめのピッキングシステム
ピッキングシステムを導入すると作業効率化が図れると説明しましたが、ここからはおすすめのピッキングシステムについてご紹介していきます。
ハンディターミナル
ハンディターミナルは、2次元コードやQRコードを読み込む技術です。バーコードをハンディターミナルで読み込み、出荷指示情報の商品であるか確認することができるので、出荷ミスを減少させることができます。リストピッキングを採用している企業で、ハンディターミナルは導入されています。
RFID
RFID(Radio Frequency Identification)は、個体識別情報を埋め込んだICタグを利用して無線通信を行う技術です。RFIDを活用することで、至近距離からの読み取りだけではなく、遠距離からの読み取りが可能となりました。また、バーコードのように1点1点商品情報を読み取る必要がなく、一括で複数の読み取りが可能です。
大量の商品情報を1度に読み込むことができるため、大幅な作業効率化が見込めるとして、大きな注目を集めているソリューションです。
2020年にはRFIDタグの情報を読み取り、「何が」「どこに」「どれだけ」あるかをデジタルマップ上に表示できる在庫管理システムLoucusMappingが登場しました。ピッキング作業の探索時間を効率化することができます。
【東日本旅客鉄道株式会社】入出庫/棚卸し/探索の作業時間の60~90%を削減!
デジタルカート
デジタルカートは、タブレット端末などが搭載されたピッキングカートです。オーダー数に応じて、6間口から12間口まで柔軟に変更できるものもあります。
カートに備えられた画面で、棚移動から商品投入までナビゲートしてくれるので、従業員教育が不要で、早期戦略化も図れます。また、ピッキングリストの印刷待ち時間や配膳などの時間短縮も見込めます。
可動式棚
倉庫ロボットと呼ばれる可動式棚が登場しました。ピッキング作業者が棚を回るのではなく、商品棚がピッキング作業者の場所まで自動的に動いていきます。可動式棚を導入すれば、ピッキング作業にかかるプロセスが大幅に省略されると大きな注目を集めています。
ピッキング業務効率化で押さえたい最新情報
デジタルピッキングの登場によって、ピッキング作業は効率化されてきました。近年では、物流を自動化するロボットも登場しています。最新情報も押さえておきましょう。
ロジスティクスロボット市場動向
富士経済が発表したレポート「様々な業界で広がる業務・サービスロボットの世界市場を調査」では、ロジスティクスロボット市場は、2017年の1,000億円から2025年までに2兆400億円に伸びると予測されています。
物流業界は労働不足が問題視されているので、人とロボットが協働する、省人化物流センターが登場しています。今後は、Eコマースによる多品種少量発注が増加しているため、併せてロジスティクスロボット市場も伸びていくと予測されます。
最近ではキヤノンが独自の映像解析技術でAGV・AMR市場への参入を発表するなど、異業種からの新規参入も活発化しています。
参考資料:次世代AGV・AMRなどの移動ロボット市場に参入「移動ロボットの眼」となる映像解析ソフトウエアを提供開始
物流業界を中心に「GTP」が普及
ロジスティクスロボット市場が拡大している中、GTP(Goods to person)が話題になっています。GTPとは、ピッキング作業者のいる場所まで荷物を運んでくるロボットや自動倉庫型システムのことをいいます。
ピッキング作業者が倉庫を移動せずに、定位置でピッキングすることができます。GTPタイプのロボットには、ButlerやEVEなどの棚搬送型ロボット、自動倉庫型システムには、Autstoreなどがあります。
GTPを採用したスマートな倉庫が登場
大手企業を中心に、GTPを採用したスマートな倉庫が登場しています。国内では、2016年にアパレル最大手のニトリが最初に導入しました。ニトリでは自動搬送ロボットとAIによって、物流倉庫の入出庫・発送業務の自動化を加速させています。
ニトリは、自社物流システムにブロックチェーンを使用した新システムを稼働させることを発表しています。個人宅配送も内製化することを発表し、大きな話題を集めました。今後スマート工場の登場で、商品企画・製造・販売・配送まで内製化する企業が増える傾向は続いていくでしょう。
参考資料:日経新聞「デジタル物流、ニトリ変身 秋にもブロックチェーン稼働」
まとめ
本稿では、ピッキング指示の課題と解決方法について解説しました。従来は、リストピッキングが主流でハンディターミナルを使って検品してきました。現在も、このような手法でピッキング作業をしている企業も多く存在します。しかし、物流業界は人手不足の問題を抱えているため、業務効率化を検討していかなければならない状況にあります。
近年では、商品情報を一括で読み取れるRFIDやピッキング作業者の場所まで自走する可動式棚が登場しています。このようなデジタルなピッキングシステムを採用すれば、業務効率化が図れるでしょう。
ピッキングに課題を感じている方は、デジタルなピッキングシステムの導入を検討してみてください。
こちらの記事では、RFIDについて、解説しています。ぜひご覧ください。
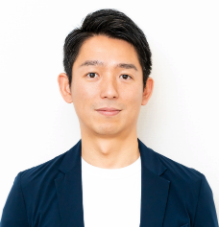
RFルーカス 代表取締役社長。
京都大学法学部卒。ノースウェスタン大学ケロッグ経営大学院にてMBA取得。丸紅株式会社にて石油・天然ガスのトレードや海外の事業投資などに従事。4年間のカタール駐在経験あり。2017年7月に株式会社トライステージに入社。事業開発部グループマネージャーとしてM&Aをリードすると共に、株式会社日本ヘルスケアアドバイザーズやメールカスタマーセンター株式会社の取締役を兼任。